Intersurgical is a truely integrated business, from design concept to our supply chain to fulfil our customer requirements. Find out more about some of the key elements of our integrated business below.
Related Pages
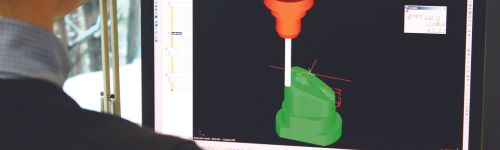
Design
We believe the best way to maintain the highest standards in design, manufacture, quality and customer care is to have complete control of these elements of our business. This integrated in-house philosophy means we are able to respond quickly and effectively to our customers and consistently meet their requirements.
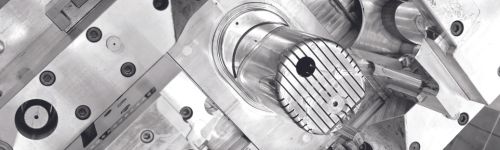
Tooling
The designs are then transferred to our state-of-the-art tool room, where the moulds are designed and validated. These tool designs, with up to 1000 individual parts, are transferred using CAM to the latest CNC tool manufacturing equipment and innovative processes such as laser sintering is used to create optimised cooling for high volume manufacture.
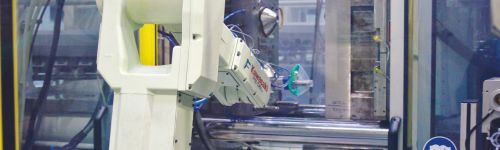
Product engineering
New moulds are trialed and validated in pre-production, and the in-house production development team design and manufacture the required assembly equipment, with an emphasis on automation. After the required trials these tools pass seamlessly into the main production area.
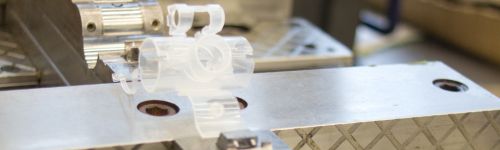
Manufacturing equipment
Intersurgical has continuously invested in new machinery, from high quality manufacturers or built in-house by our engineering departments across our manufacturing sites.
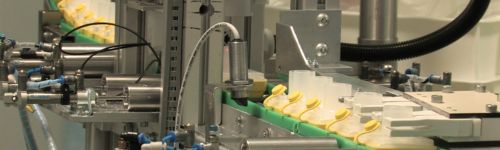
Manufacture
We use all of the conventional moulding techniques within the company, for volume manufacture of over 97% of the component parts that are utilised in our finished products.
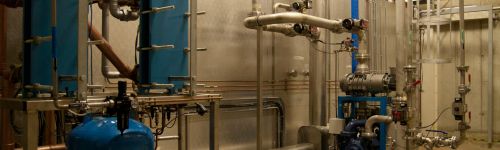
Sterilisation
Products that require sterilisation are moved into a separate area of a factory to undergo sterilisation treatment using Ethylene Oxide.
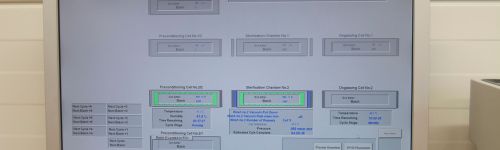
Information Technology (IT)
Information technology is an integral element of the total manufacturing control process, our MRP database forms the backbone of a system that delivers information for production right to the operatives work place with details of product formulations, work instructions and quality requirements. The deployment of this all forms part of the e-learning system, essential to ensure consistent product quality.
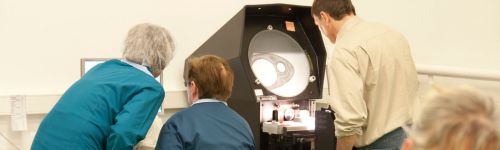
Quality
All of our products are designed and manufactured to meet or exceed the requirements of relevant BS, ISO and EN standards and are regularly audited by the relevant bodies.
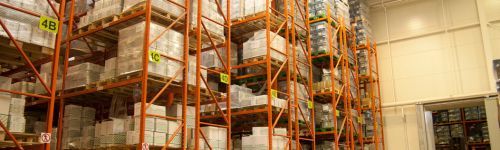
Stock and supply
Having stock in the right place at the right time is imperative for a consumables business. It is essential that we are able to reliably supply our customers and that they can trust we will meet their requirements. Local warehousing and distribution allows quick and efficient delivery to our customers worldwide.
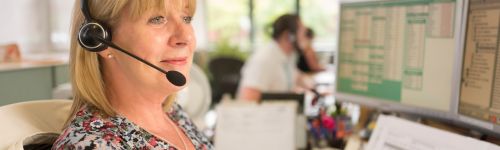
Customer Support
Our sales and marketing network is extensive and effective, with 28 direct sales subsidiaries around the world, covering our key markets and a network of speciality distributors. Intersurgical staff globally are ready to support our customers requirements, in the shortest possible period, with efficient supply, training, clinical information and support.